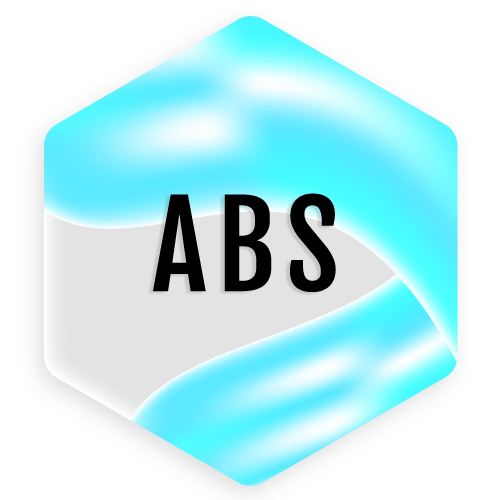
WHAT IS ABS?
For more than 70 years, ABS has been used to make a variety of industrial parts and consumer goods from automobile dashboards to LEGO® bricks. ABS yields more durable, impact-resistant parts than other industrial plastics. Aesthetically, ABS comes in many colors, is easily injection-molded, and achieves high-quality finishes.
For the same reason, ABS filament is a popular choice for commercial and enthusiast markets. ABS produces printed objects that can withstand handling and everyday temperature conditions. However, ABS does require more performance than many entry-level printers can provide. Let’s look at why Hatchbox ABS remains such a popular choice.
HOW WAS ABS FIRST MADE?
Acrylonitrile Butadiene Styrene, or ABS, was first made in the 1940s as part of the wartime effort to create artificial materials. Styrene-acrylonitrile (SAN) was already being used to make containers and other rigid objects. Styrene provided hardness and acrylic provided strength but SAN-based objects were brittle. Polybutadiene, on the other hand, was developed to replace rubber for use in things like tires. ABS combined the properties of SANs and polybutadienes to make objects more durable and impact resistant.
While polybutadiene does not blend well with SAN, there are ways to get them to work together. The original approach created an emulsion of butadiene polymers and acrylonitrile and styrene monomers. The exact ratio of the three components as they polymerized would determine the properties of the final ABS blend.
HOW ABS IS MADE TODAY
Modern ABS manufacturing uses a mass-production process that chemically bonds acrylonitrile to a backbone copolymer of butadiene-styrene. This process gives manufacturers more control over the acrylonitrile-butadiene-styrene ratio and the resulting material properties. Styrene typically comprises half of the mixture with butadiene and acrylonitrile making up the rest.
Additives further modify these properties to provide, for example, greater UV resistance. Pure ABS is a translucent white, but dyes and pigments let suppliers offer products in a variety of colors.
ABS is easily injection-molded and can be made to a high-quality finish which makes it popular across many industries from household goods to automotive parts to electronics. The same properties make ABS 3d printer filament a common choice for 3D printing.
CAN ABS BE RECYCLED?
ABS can be melted and reformed without losing its properties.Theoretically, this makes ABSfully recyclable. The reality is different. Like polycarbonate, nylon, and other plastics, ABS falls under Plastic Resin Code 7. As a result, many recycling facilities receive ABS in lots mixed with many other materials.
Melting ABS with other plastics will contaminate the recycled material and severely constrain how it can be used. Unless the recycling facility has processes that can separate ABS economically, it will endup in landfills or incinerators. For this reason, a lot of research is going into froth flotation and other new technologies that can separate ABS efficiently.
If you use a lot of ABS, consider recycling it yourself by shredding your ABS scraps and melting it into fresh filament. Your local maker space may have the equipment you need.
WHAT IS FROTH FLOTATION?
First developed by the mining industry in the 19th Century, froth flotation is a method of separating minerals such as graphite, sulfides, and gold from ores. The process takes advantage of a mineral’s hydrophobicity, its ability to repel water.
First, the ore is crushed and ground until into fine particles where each grain is a separate mineral. After mixing the particles with water to form a slurry, specially tailored chemicals are added to make the target mineral more hydrophobic. Chemical and mechanical churning aerates the slurry and captures the hydrophobic minerals to the bubble walls.
The resulting froth rises to the surface and gets skimmed off to extract the target minerals. Froth flotation lets mining companies extract minerals from ores in higherconcentrations and makes their operations more profitable.
HOW IS FROTH FLOTATION CURRENTLY BEING USED?
Froth flotation is also a common process in the recycling industry.Wastewater treatment plants use froth flotation to remove fats, oil, grease, and other hydrophobic solids suspended in household and commercial wastewater. Some paper recycling plants use froth flotation to remove inks and other hydrophobic contaminants.
Researchers have looked at using froth flotation to separate ABS from old cars. In America, the Argonne National Laboratory built a pilot plant in the early 2000s that separated ABS from automobile shredder residue. The European LIFE PlasPLUS project plans to do the same.Both projects focus on automotive plastics because old cars are a concentrated source of thermoplastics like ABS. Europe’s car industry, for example, accounts for 15% of the continent’s plastic production. Froth flotation could make ABS recycling profitable.
ABS INDUSTRIAL USES
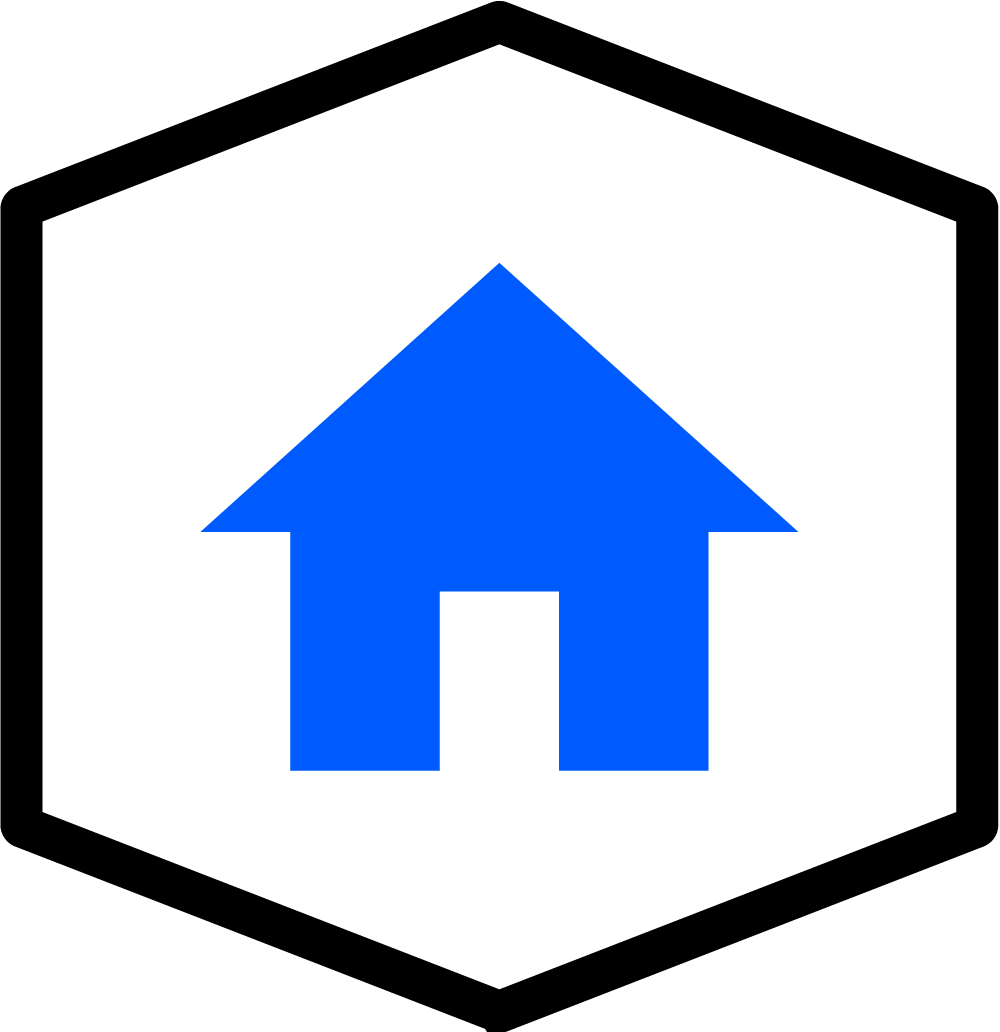
HOUSEHOLD AND CONSUMER GOODS
Kid-safe and durable, ABS’ natural translucent-white color readily accepts pigments and dyes. As a result, you will find ABS parts in products throughout your house. This is why LEGO® bricks, for example, have been made from ABS since the 1960s. ABS is also used in wastewater drainage pipes because of its corrosion resistance.
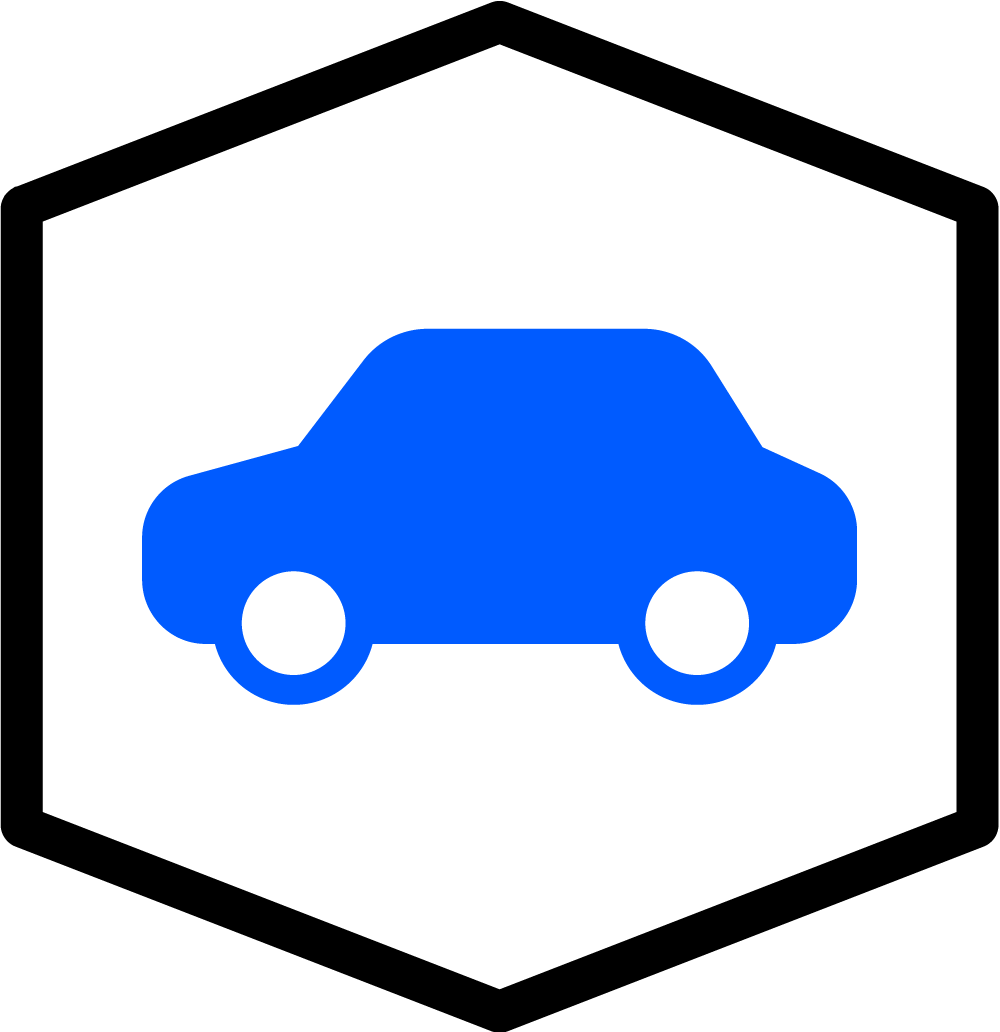
AUTOMOTIVE
Some plastics suffer in the wide range of temperatures inside and outside a car. Combined with its strength and durability, ABS’s temperature resistance makes it the automotive industry’s preferred choice for engineered plastic parts. With the right formulation, ABS-made car parts also resist exposure to ultraviolet light.
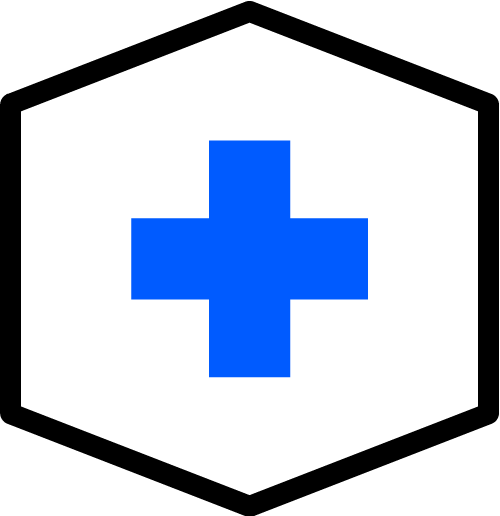
MEDICAL
ABS has found widespread use in healthcare and pharmaceuticals. The biocompatible material can be used to make prostheses, drug-delivery systems, and other devices. Compatible with gamma-ray, ethylene oxide, and other sterilization procedures, medical-grade ABS has the durability to withstand everyday use in healthcare settings.
ABS EVERYDAY USERS & HOBBYISTS
Even though PLA is easier to work within the home or classroom, ABS remains popular among hobbyists. ABS provides more post-processing options to create better finishes. Its durability makes ABS a better choice for replacement parts and frequently-handled objects. ABS parts will also survive conditions in your car on summer days.
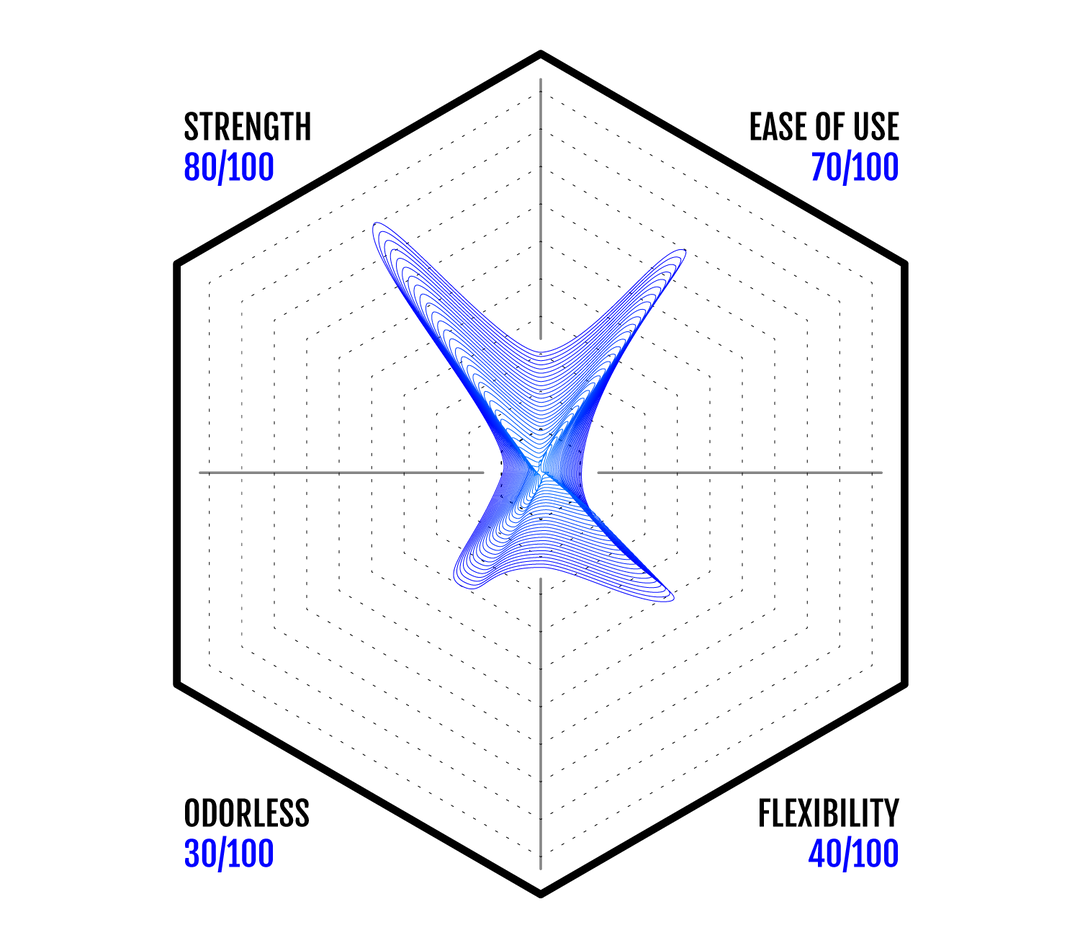
ABS PRINT SETTINGS
SIZE AVAILABILITY: 1.75MM | 3.00MM
RECOMMENDED EXTRUSION TEMPERATURE: 210°C - 240°C
PLATFORM ADHESION: Kapton Tape or Hairspray
RECOMMENDED BUILD PLATFORM TEMPERATURE: 80ºC - 100°C
ABS BENEFITS
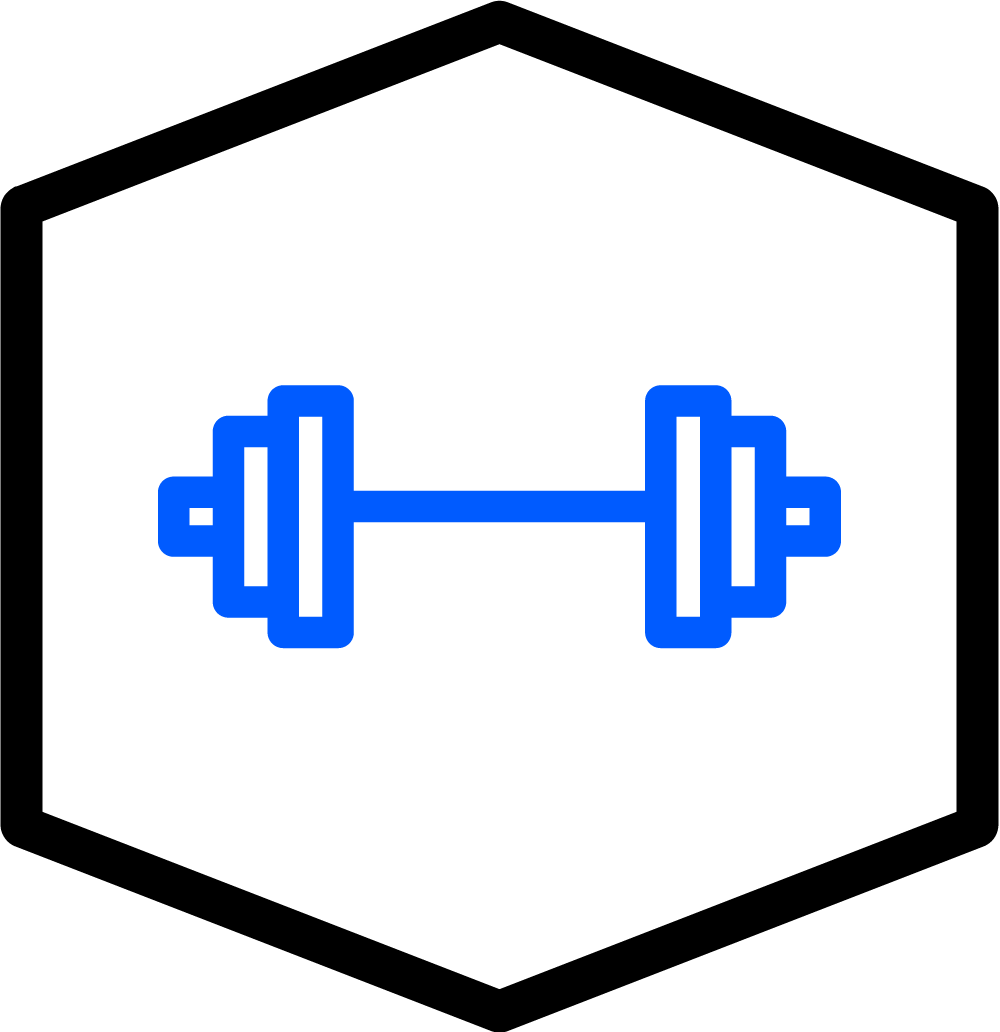
DURABLE
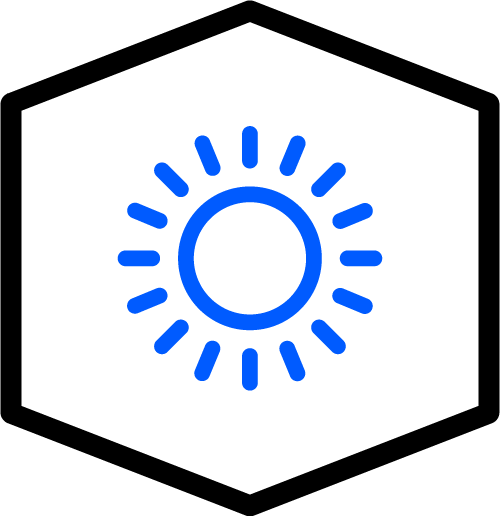
UV RESISTANT
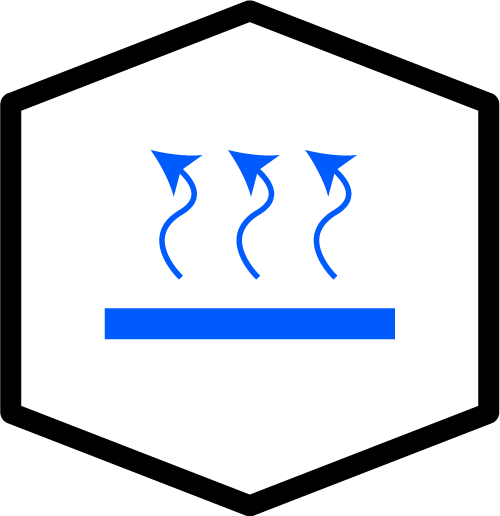
HEATING BED REQUIRED
ADVANTAGES & DISADVANTAGES OF ABS
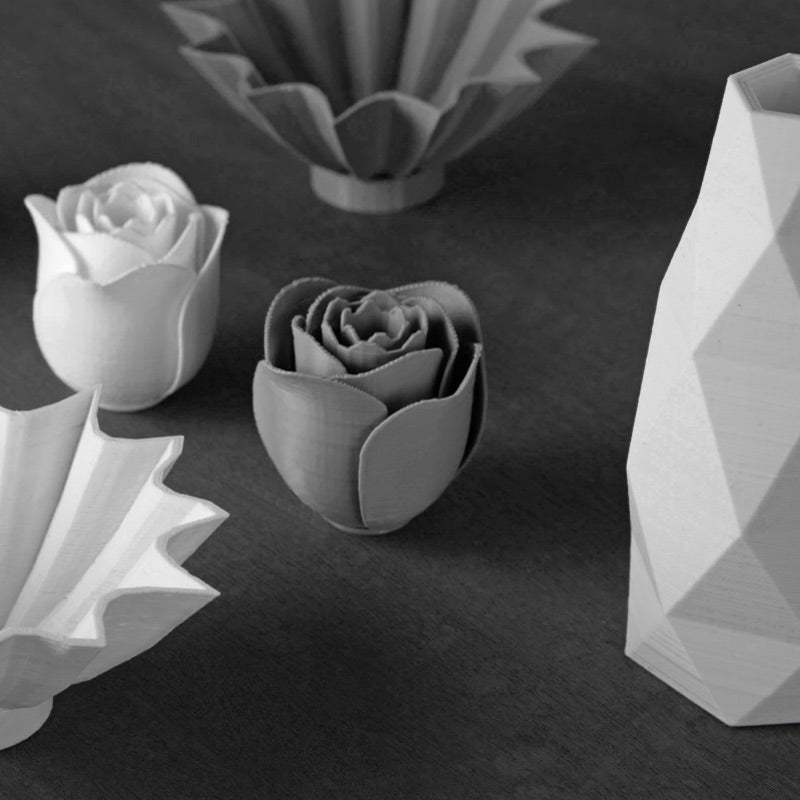
ADVANTAGES OF ABS
Objects printed with ABS are more suitable for finished applications than those printed with PLA. Greater strength, impact resistance, and heat resistance combine to make ABS parts more durable in a wider range of environments. Melted ABS creates less friction in the extruder which lets you produce finer details on small parts.
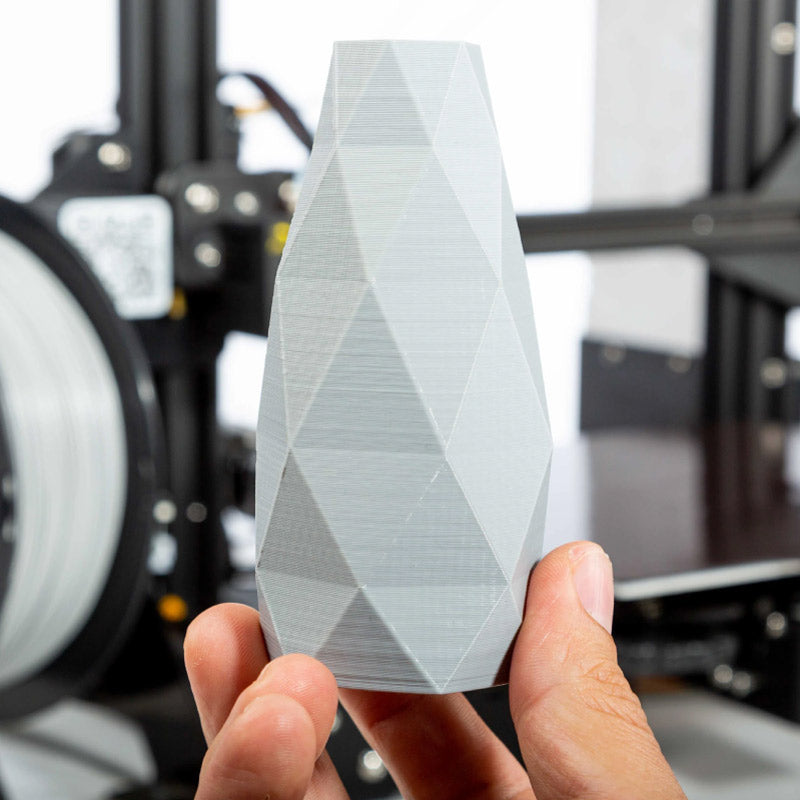
DISADVANTAGES OF ABS
While cooling, ABS contracts as much as 2%. Medium-to-large objects may run into bed adhesion or layer separation issues during the print job. Although not toxic in small quantities, vapor emissions during printingsmell bad enough to require a ventilated space. Other disadvantages include UV-sensitivity and humidity-sensitivity.
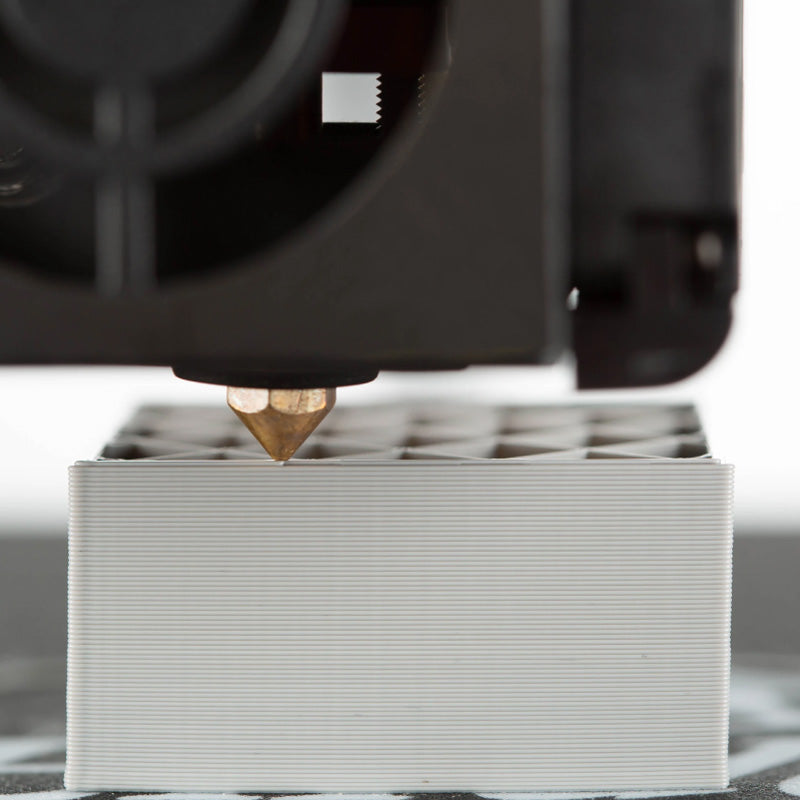
ABS PRINTING TIPS
Set the extruder to 210-240°C and the print bed to 80-100°C. High bed temperatures, bed coatings like ABS slurries, and temperature-controlled enclosures will help prevent adhesion and layer separation. ABS dissolves in acetone which lets you use post-processing techniques like acetone smoothing and solvent welding.